Manufacture
AMAC Corrosion manufactures an enormous range of anodes, from simple catalogue items such as 0.5 kg yacht hull anodes to 4 tonne bracelets specifically designed for offshore pipelines. AMAC Corrosion's manufacturing facilities consist of specialised high output casting foundries dedicated to the manufacture of Aluminium, Lead Silver, Magnesium and Zinc anodes.
AMAC Corrosion has accumulated many hundreds of moulds that produce thousands of anode types for every application. Our extensive range of moulds allows us to cast to almost any dimensions. Our versatility is what sets us apart. Numerous variables such as mould temperature, humidity, casting temperature, casting technique, alloy composition and insert material affect the quality of the anode. If the preparation or materials are not correct, anodes may crack, cold shuts may develop or any number of problems may occur that affect the quality of the anode. AMAC Corrosions dedicated team of production staff have an exceptional understanding of sacrificial anode manufacture based on knowledge accumulated over more than 25 years. Anode Purity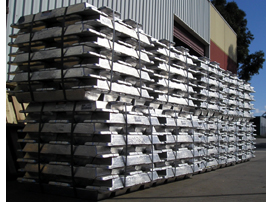 High quality anodes are dependent on the purity of the raw materials and cleanliness of the casting equipment and facilities. To ensure anode purity, all raw materials undergo thorough inspection and every alloy batch is spectrographically tested prior to anode casting. Anodes can only be cast if the spectrographic analysis is within specification.
Casting moulds must be correctly cleaned, chemically treated and preheated to the optimum temperature prior to casting. All casting equipment such as ladles and transfer pots undergo thorough cleaning and treatment to ensure no contaminants enter the anode material. If required, steel inserts are linished or sand blasted prior to casting and wire cores are purchased free of oils or lubricants to ensure that no residue enters anode material. Design and Manufacture
Engineers can easily calculate details such as current output and anode mass, but the best anode design for a particular application should be based on the expertise of Corrosion Engineers working in conjunction with the manufacturer at the design stage of a cathodic protection system. Cathodic protection systems developed at AMAC Corrosion are based on the conceptual requirements specified by Design Engineers and the reality of actually manufacturing the final product.
Assembly of Cathodic Protection Equipment AMAC Corrosion designs and manufactures monitoring hardware such as Groundbed Control Boxes, Test Point Boxes and Monitoring Posts. AMAC Corrosion has a range of standard products, all of which can be customised for individual installation requirements.
|